

每种方法都会留下不同程度的风险,导致存在助焊剂残留物,可能会导致故障。SMT焊接方式的风险最低,而使用液体助焊剂的风险最高。了解应用过程,助焊剂中的成份以及助焊剂制造商的建议可以极大地提高电子设备的可靠性。助焊剂是指能够去除PCB表面、焊料本身的氧化物或表面其他污染,湿润被焊接的金属表面,同时在焊接时保护金属表面不被再次氧化,减少熔融焊料的表面张力,促进焊料扩展与流动的化学物质。其作用是,辅助热传递、去除氧化物、降低表面张力及防止再氧化。您可能会听到“低活性”和“高活性”这两个术语,以描述焊接后的助焊剂残留物是否具有引起清洁相关故障的风险。但是,从化学的角度来看,这些术语没有准确定义,也没有单一的标准分析或化学测试将助焊剂残渣分类为“低活性”或“高活性”。这是因为泄漏电流引起的故障不仅取决于助焊剂的化学性质和施加的助焊剂的量,而且电气灵敏度和使用环境也会对可靠性产生重大影响。波峰焊,选择焊和手工焊接中使用的大多数液体助焊剂成份包括: 作用:清洁焊接表面,降低表面张力的作用。免洗型的助焊剂通常会使用有机弱酸(WOA)作为活化剂。一部分弱酸为戊二酸,琥珀酸和己二酸。活化剂的存在使焊剂残留物具有风险,因为它们是酸性的,但对于获得良好的焊点来说是必备的。它们与金属氧化物反应形成金属盐,促进润湿,并且在盐溶解后形成冶金键。在焊接过程中逐步消耗酸性物质,该酸可能会用于其他有污染或分解反应的反应中,但这些反应并不一致,取决于助焊剂的化学性质和其他不易控制的因素。大多数有机弱酸在焊接温度下基本上不会蒸发。因此,重要的是将活化剂的量(和助焊剂)调整到良好焊接所需的最小量。

成膜剂是不溶于水的高熔点化学品。焊接后,它们形成了大部分可见残留物。它们起着包含活化剂的作用,并防止它们溶解在水中。“低固态”助焊剂配方几乎不含成膜剂,几乎没有可见的残留物。从理论上讲,更多的成膜剂可以减少发生故障的风险,但同时也会使组件看起来很脏。成膜剂最常见的成份是松香,化学改性的松香和合成树脂。溶剂的主要作用是溶解焊剂中的所有成份,使之成为均匀的黏稠液体,易于使用。有时,可以使用几种具有不同沸点的溶剂来确保焊接曲线的不同温度阶段保持物理性能,必须在焊接过程中完全蒸发。如果溶剂存在助焊剂残留物中,则会增加发生故障的风险。重要的是要确保仅将助焊剂施加到组件的暴露于峰值焊接温度的区域。在波峰焊接过程中,助焊剂可以通过孔流到组件的顶侧,也可以在保护层下流过,从而不会出现在在高温下。手工施加的液体助焊剂可能会特别成问题,人为的因素影响很大。添加剂通常只占助焊剂的小部分。它们可以是增塑剂,染料或抗氧化剂。虽然制造商可能会添加化学成分来帮助提高可靠性,但其残留的影响微乎其微。
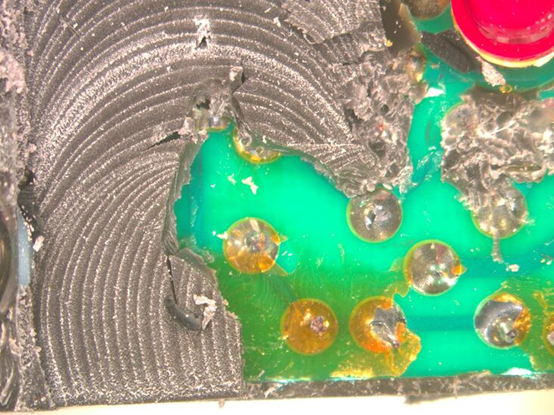
由于所使用的助焊剂的量很重要,因此这些不同的应用过程会带来与清洁相关的故障的风险等级不同。锡膏助焊剂的风险最小,这是因为使用网板或印刷机来控制锡膏助焊剂的施加量。表面贴装中回流焊残留物造成的故障很少(QFN可能有问题)。液体助焊剂的使用则带来更大的风险。喷射使用比其他过程可使用更多的助焊剂。如果未进行最佳控制,则该工艺可能会施加比所需更多的助焊剂,从而留下更多的酸性残留物,为潜在的化学腐蚀反应创造更有利的条件,而且液体助焊剂也可能会流向未处于高温下的部分。控制手工焊接过程中施加的助焊剂的量也可能很困难,过量的助焊剂可能在附近的组件下流动,人工熟练程度影响很大。
助焊剂残留物指的是焊接后不挥发成份、残留的活性成份以及生成的金属盐类。

助焊剂残留物的种类:PCB焊接后残留物的产生与焊接过程中使用的助焊剂类型有密切的关系,从使用的助焊剂类型来看常见的残留物主要分为以下两类。- 松香焊剂的残留物:主要是由聚合松香、未反应的活化剂以及焊接时松香与熔融的焊料之间反应生成的盐等组成。
这些物质在吸潮后体积膨胀,部分物质还与水发生水合反应。这些呈白色或褐色的残留物吸附在PCB上,清除异常困难。
- 有机酸焊剂残留物:如目前广泛使用的免洗助焊剂,其主要由多种有机酸组成,也包含一些在高温下可以产生卤素离子的化合物。
这类残留物最难除去的是有机酸与焊料形成的盐类,它们有较强的吸附性能且溶解性较差。
最常用的评判助焊剂残留物的方法是表面绝缘电阻测试和电化学迁移测试。尽管没有一个能进行全面风险评估的工具,但是有一些风险评估方法能成功的降低失效的风险。通常在SMT清洗操作过程中通过溶剂萃取物(ROSE)的电阻率来间接判定助焊剂残留离子的清洁度,数值结果有助于确保合格的焊料和清洗过程。离子色谱法IC已成为一种常用的技术,用于识别SMT表面上的常见离子,并提供焊接后残留的有机弱酸活化剂含量的直接测量值。对于液体助焊剂尤其重要,因为可以很容易地检测出所施加的助焊剂量,不同的离子色谱方法产生不同的结果。完整的组件浸泡测试为整个组件表面上检测到的平均的离子浓度,而局部提取技术则可在小范围内测量离子浓度。
对于可靠性要求比较高的电子产品,焊接后必须经过严格的清洗工艺。为了降低清洗的难度,在PCB完成焊接后应尽快进入清洗工序,在清洗时既要针对非极性残留物也要针对极性残留物,因此需使用极性与非极性的混合溶剂来清洗才能有效除去残留物。当然,必须选择完全合规的环境友好型清洗剂。
理想的助焊剂应该具有高活性、低腐蚀性,然而两者却是彼此对立的指标,常常有很多助焊剂在一味追求高活性的同时忽视了其腐蚀性。因此在面对诸多的助焊剂时,有必要进行实际的焊接工艺试验来选择性能良好、可靠性高的助焊剂。
在保证焊接质量的前提下,焊接过程中应适当提高预热温度和焊接温度,保证必要的焊接时间,使助焊剂中的活性剂及溶剂尽可能多的随高温分解或挥发,减小焊后残留物。

